Energy absorbing metamaterial
Introduction
Materials engineering is important for nearly every type of physical invention. Every industry, from agriculture to aerospace, requires materials with specific properties to allow engineered systems to function precisely and accurately.
There has always been interest in the development of materials with extreme damping capabilities. Damping is the ability of a material to absorb energy in a desired pattern or time frame. It is used to prevent vibrations in motors, protect objects from breaking when dropped, and stabilize objects once they reach a certain force threshold.
The absorption of energy is determined by the area under the stress-strain curve for a given material through integration. Every material has a yield strength and an ultimate strength (shown in an example stress strain curve below). Once the material has been stretched or compressed past the yield strength, it will no longer exhibit elastic behavior and will never return to its original size and shape.
Super elastic materials are materials that have high damping capabilities and can withstand large strains while not exceeding their yield strength and therefore maintaining their reversibility. Metamaterials are materials composed of small mechanisms that allow the material to have different mechanical properties than the material otherwise would on its own. This opens the door to the development of structures and mechanisms that have very specific properties such as large strain, and high damping. No chemical synthesis is required to construct these materials. A couple of past metamaterial projects from the interactive structures lab are shown on the right.
Objective
Carnegie Mellon’s interactive structures lab set out to create a super elastic metamaterial with reversable high damping capabilities. We aim to create a material with a similar stress-strain curve to nitinol, but more than double the amount of recoverable strain, therefore, increasing the damping capabilities by over 100%. An example of the desired stress-strain curve is shown below.
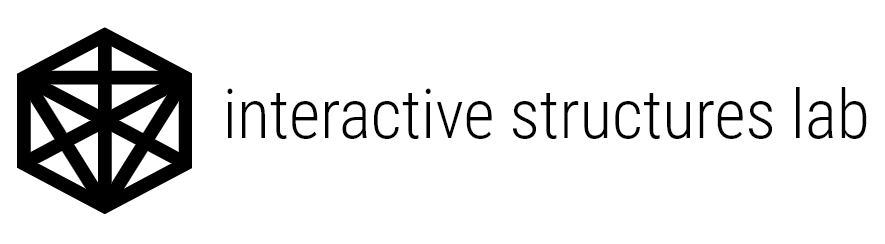
Design
The design of the material involved networks of cells made fabricated from thermoplastic polyurethane (TPU) which is a flexible 3d printing filament. The grids were designed using SolidWorks and finite element analysis (FEA) was performed to obtain force displacement curves, stress heatmaps, and maximum strain values.
The makeshift spring contains a rigid fork, connected to a thin buckling member spring that after a small delay, snaps back to its original position. We will refer to this behavior as ‘barely bi-stable’. There are two states, but one is more stable than the other. This means the spring will always return to its original state without needing to apply an opposite force, even if it stays in the second state for a few moments. Below are stress-strain curves for uni-stable, ‘barely-bistable’, and bistable mechanisms.
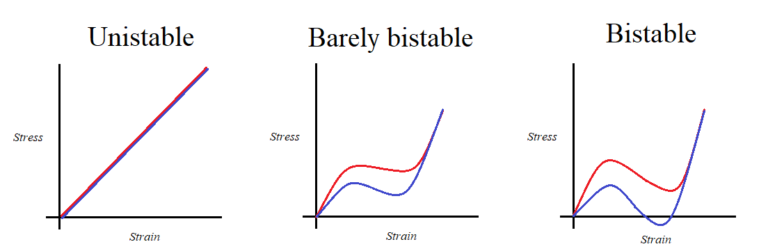
When these mechanisms are connected as a metamaterial in large grids, the material can exhibit very high strains due to the deformation of the buckling members from the springs. Concept pictures are shown below:
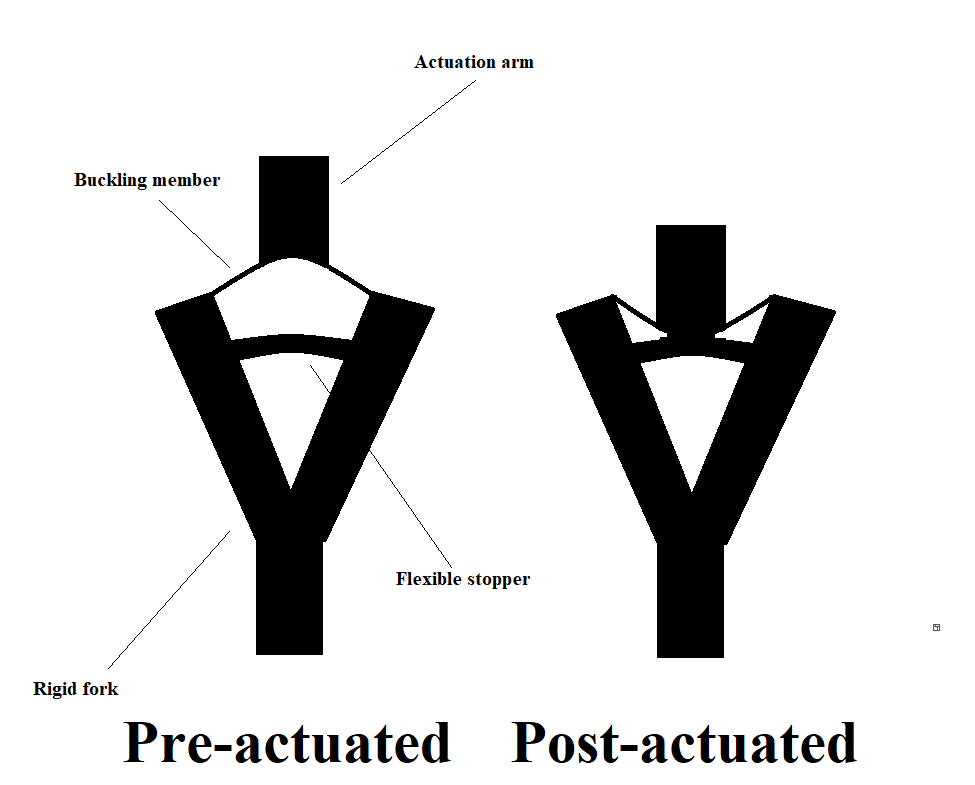
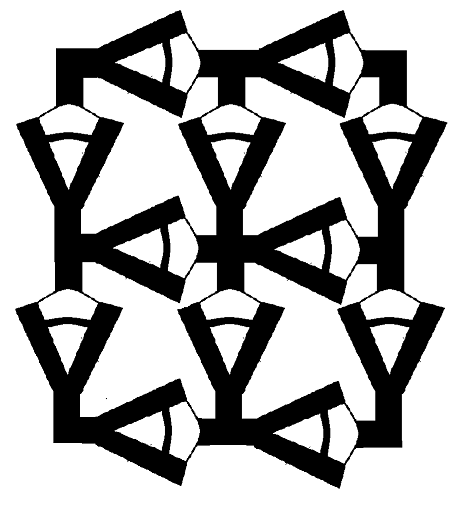
Final Prototype
A final prototype was reached after 4 generations of spring mechanism prototypes and 3 different mesh configurations. The final mesh consisted of square cells will springs on each side. Small strings in a cross pattern were attached to inside of cells to prevent the shearing of the material when compressed, making it easier to each of the spring to buckle.
Testing
Force displacement tests were performed to determine the shape of the stress and strain curve of the material.
By observing these stress strain curves and comparing them with the stress strain curves of other springs, it is clear from the area contained within the loading and unloading curve that the material has high absorption capabilities.
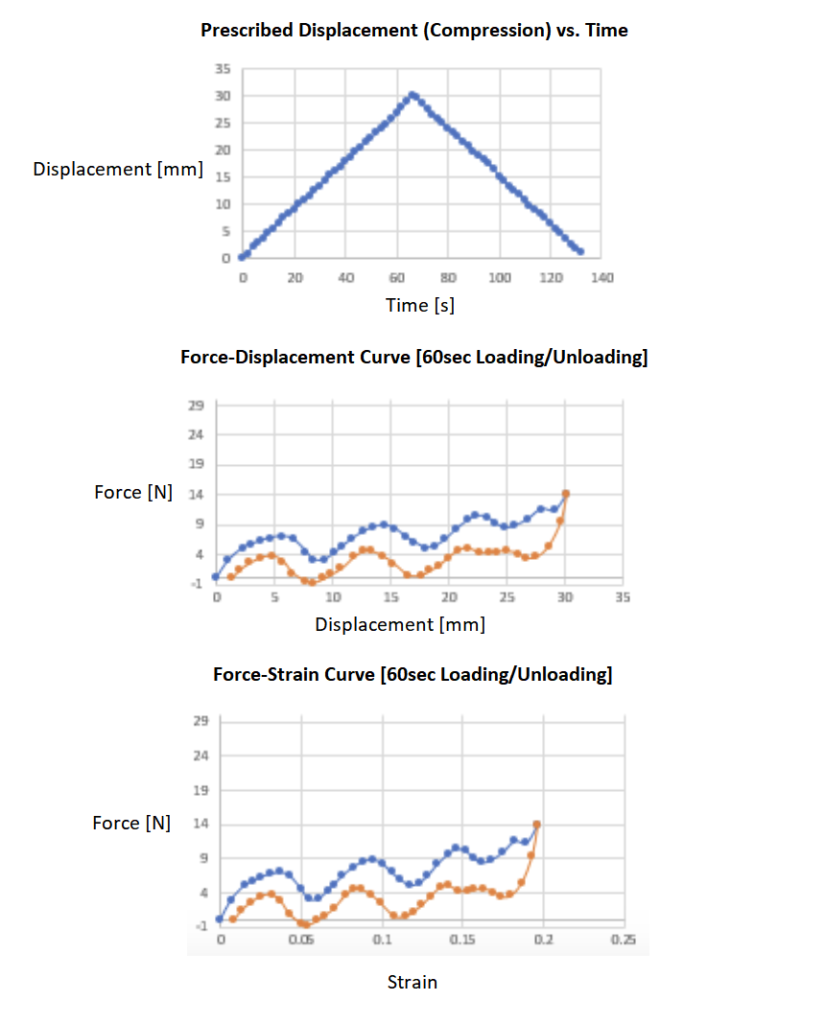
Applications
Damping materials have a wide range of applications from vibration control to protection of objects and people through energy absorption. The material could be implemented into football and hockey helmets to absorb any force above a level that is safe for players’ heads. It could also be used in the crumple zones of cars to absorb energy and return to its original shape incurring minimal damage to the car’s body.
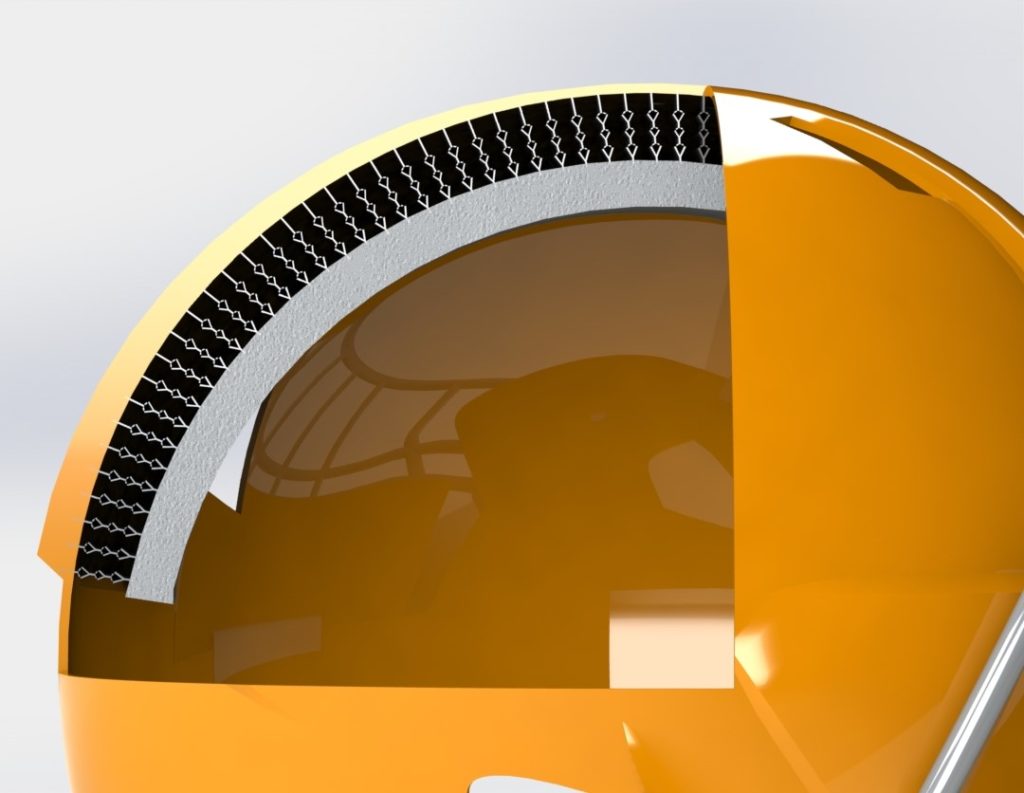
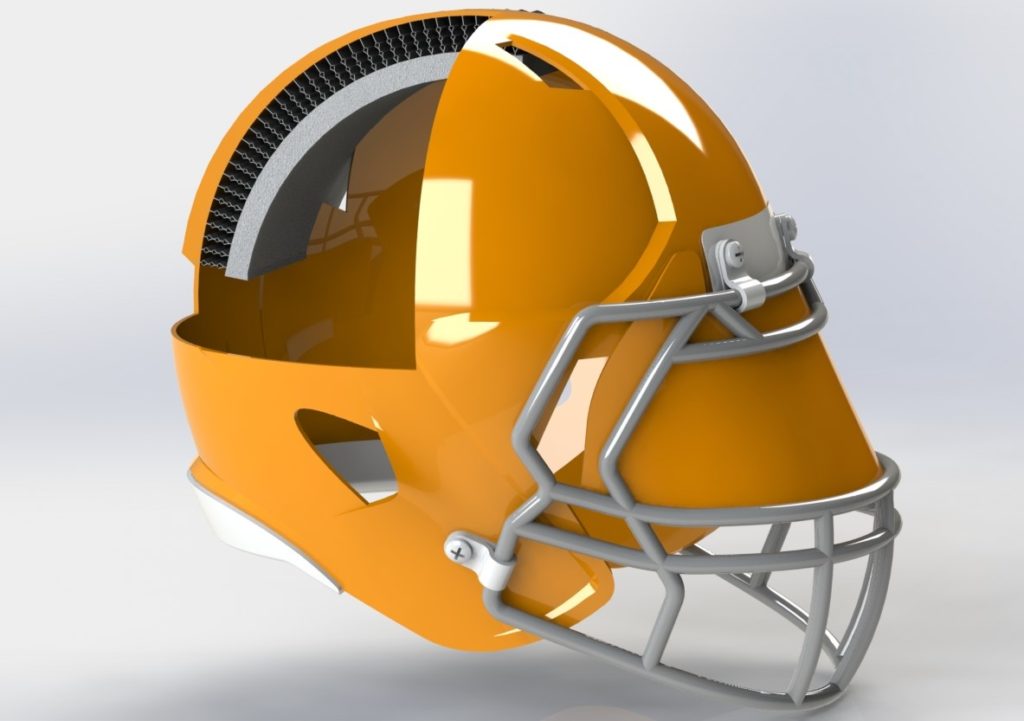